Before discussing on the SAP PM (Plant Maintenance) module let’s read SAP PM overview and understand what Plant Maintenance is. If we take any manufacturing industry or assembling plant, many machines and equipment are installed in the plant. These machines continue to function as long as they are in good condition and would stop working if something went wrong (nothing but breakdown of machine). So to avoid this breakdown, the team involved in up keeping of machines are called maintenance personnel/team. The prevention work they do is usually known as preventive maintenance and the repair work they do when a machine broke down is breakdown maintenance. This classification is in very broad way and we will discuss in detail as process further in SAP PM course. Maintenance function is called in different names as per their convenient or geographical region wise namely – Maintenance, Plant Maintenance, Plant Engineering services, Facility management, and so on.
As we have seen in the paragraph above, for smooth running of a plant and machineries, the plant maintenance function plays a very important role. In SAP ERP, maintenance function will be covered with SAP PM module. This will be implemented for smooth and systematic running of plant maintenance function and to capture different reports. These reports are generated by automated capturing of equipment history, maintenance works, labour cost, material consumption, and so on. Ideally these reports will be useful in tracking consumption of material, manpower, and costs. Having this data we can monitor and reduce the maintenance cost or material consumption wherever possible and in turn increase the company profits. Let’s see this in detail how this works.
SAP PM Organizational Structure
SAP PM overview cannot be complete without the information about organizational structure adopted by this module. In any company that implements SAP PM module, the organizational structure is subdivided in to the following format using the same hierarchical level as demonstrated below.
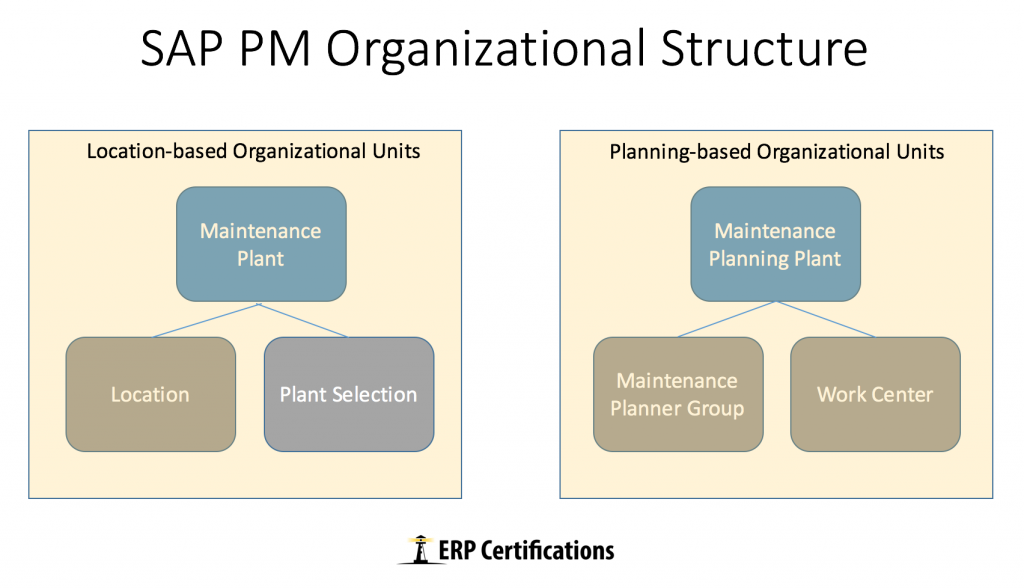
Once the client decides to implement the SAP PM for their Organisation, they will decide for which plant they wanted to do it . This is because they may be having the 3-4 plants in different locations or cities and out of which the management decides for which plant they wish to implement SAP PM. Once this decision is made project kick off will takes place and the project will be implemented using ASAP methodology.
Overview of SAP PM
While implementing SAP PM module, first thing is to design and define the Organisation elements along with other components in master data of PM. We need to configure in certain areas for different master data components wherever it is applicable as per the business needs and upload the master data into the system. Let’s see the master data components mentioned below:
- Work Centers
- Functional locations
- Catalogs
- Equipment
- BOMs (Bill of Materials)
- Characteristics
- Classification
- Measuring points
- Permits
- Revision
Having complete information about these master data objects gives one a complete SAP PM overview in terms of how a company is structured.
Plant Maintenance Business Processes
Forecast
Detailed study of machineries and budgeting for the same on maintenance cost which includes:
- Internal labour
- External labour
- Service contracts
- Spares
- Capital equipment expenses
- etc
for the complete maintenance function. Annual planning of preventive maintenance for machineries will be done based on machine manufacturer recommendation and maintenance personnel prior experience.
Maintenance planning
Detailed planning for the preventive maintenance schedule like daily, weekly, half yearly, yearly etc. And capacity scheduling.
Execution on planned maintenance
Planned maintenance process are converted in to preventive maintenance work orders as per the planned maintenance schedule and these orders are executed as per the plan.
Execution on unplanned maintenance
Creating of work orders for the machine stoppages are unplanned maintenance, nothing but breakdown orders and executing these orders.
Report generation/capturing
Relevant data & reports can be captured from the system like:
- Breakdown hours
- Equipment history
- Order status
- Cost
- Labour hours
- Spares consumption
- etc.
SAP PM Integration with Other Modules
Work Centers
Work centers are nothing but set of people who carry out the maintenance task in Plant Maintenance. There can be different types of work centers like Mechanical, Electrical, Instrumentation etc. So, this is the integration with HR module. Each work center will be having different wages or rates per hour which is nothing but cost. So this is the integration with CO module.
Bill of Materials (BOM)
This is bill of material which means materials are used in Equipments which in turn, list of items maintained in material master, nothing but integration with MM module. Certain testing equipment or instruments are need to be calibrated at regular intervals. This is carried out through calibration orders. This is the integration of SAP PM and QM modules. For typical investment or capital orders (maintenance orders) a budget is allocated from a finance team. This is the integration with FI module. In production area, equipment is considered as the work centers (only to production area equipments are work centers, whereas for PM they are technical objects) and their respective work center details will be maintained in equipment master data. This is an integration with SAP PP module.
We will learn more about this integration part in detail as we move further from SAP PM overview to the upcoming chapters.
Leave A Comment?
You must be logged in to post a comment.